Textile making techniques are important because they are the fundamental basis for obtaining perfect finishes in your productions of various garments.
1) Normal screen printing and relief screen printing
Screen printing, also known as silk screen, is a printing process. In this technique of textile making, which can be carried out by a person, mechanically, or automatically, by machines, the ink is poured, by means of the pressure of a squeegee. This squeegee is passed along a screen (made of nylon or silk), which is stretched on a wooden or steel frame.
Today, screen printing is one of the most common textile manufacturing techniques for printing T-shirts, shirts, pants and other garments. In addition to fabrics, screen printing can be used for printing on various types of materials, such as plastic, rubber, paper, wood and glass, and surfaces, such as spherical, cylindrical, irregular, opaque and glossy. In addition, there are different thicknesses and sizes that can be used as a base for the various types of screen printing inks.
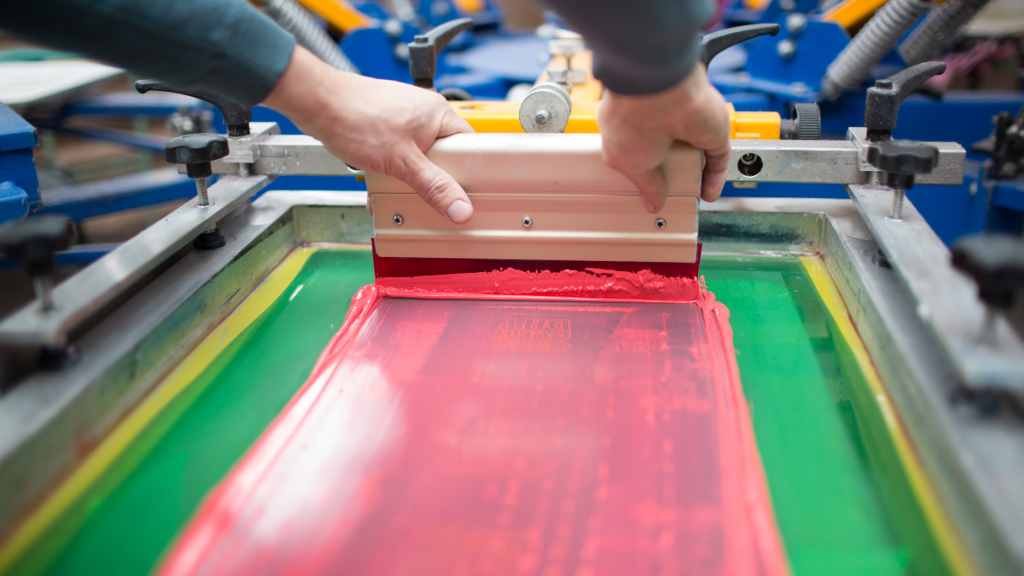
2) Strass
Strass is a textile manufacturing technique widely used in party clothes, fashion accessories and even in furniture and decorative objects. This textile manufacturing technique consists of applying crystals or synthetic stones to surfaces, forming elaborate designs or patterns.
Rhinestones can be a great way to add a touch of luxury and sophistication to your work. Compared to some textile making techniques, Strass is a relatively easy technique to learn and can be applied to many types of fabrics, from the lightest to the heaviest.
The origin of its name comes from the first man to produce this stone, the Frenchman George Friedrich Strass, with the intention of creating something with a diamond-like shine. It is still a crystal because it is made from shards of glass or plastic dissolved in metal powder or film.
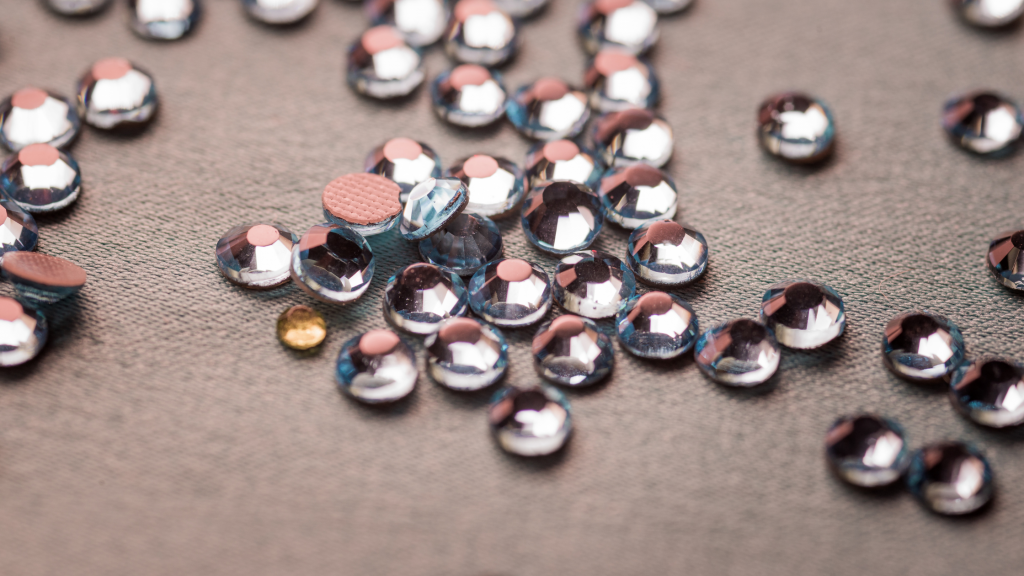
3) Induction
Induction textile manufacturing is a welding method that uses electromagnetic energy to fuse or bond textile materials. It is a relatively new technique and is not yet very common in the textile industry.
The induction welding process works by generating a magnetic field that generates heat in the materials to be joined. This technique is especially useful for joining synthetic materials such as polyester, nylon and other thermoplastic materials.
To use the induction textile manufacturing technique, you need two pieces of fabric that will be joined together. The parts are placed in a press where a magnetic field is generated, heating the parts to the melting point. When the parts fuse, the press is turned off and the parts are removed.
The induction textile manufacturing technique is able to join materials very quickly and efficiently, without the need for seams or other mechanical joining methods. This can lead to greater durability and strength of textile products and allows for the non-use of chemicals, making it a greener option for textile production.
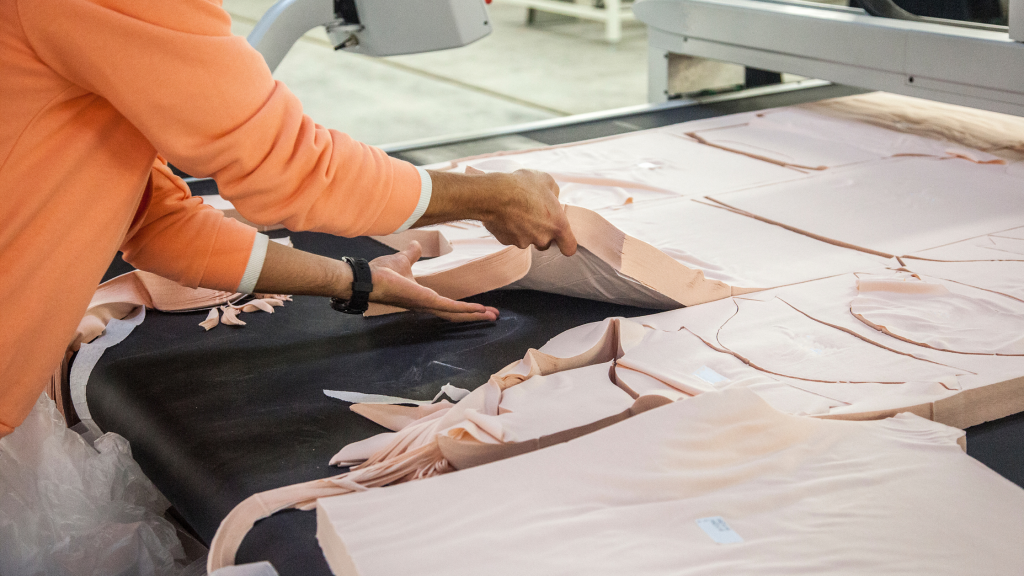
4) High frequency embroidery
High frequency embroidery is an advanced embroidery technique that uses special high frequency equipment to produce complex and detailed designs on fabrics.
In this technique, special embroidery equipment is used to produce designs at high frequency, which means that the embroidery needle penetrates the fabric several times at high speed, producing a three-dimensional effect in the design.
The high frequency embroidery process starts with the creation of the digital design in a specific software. The fabric is then fixed in a hoop and the machine is programmed to follow the design and create the embroidery.
One of the main advantages of this technique is the ability to produce complex and detailed designs on a variety of fabrics, including thick and stretchy fabrics. This technique allows the embroidery to have a high relief, providing a three-dimensional appearance.
However, it is important to point out that the high-frequency embroidery technique requires a specialized equipment and experienced professionals to operate it properly.
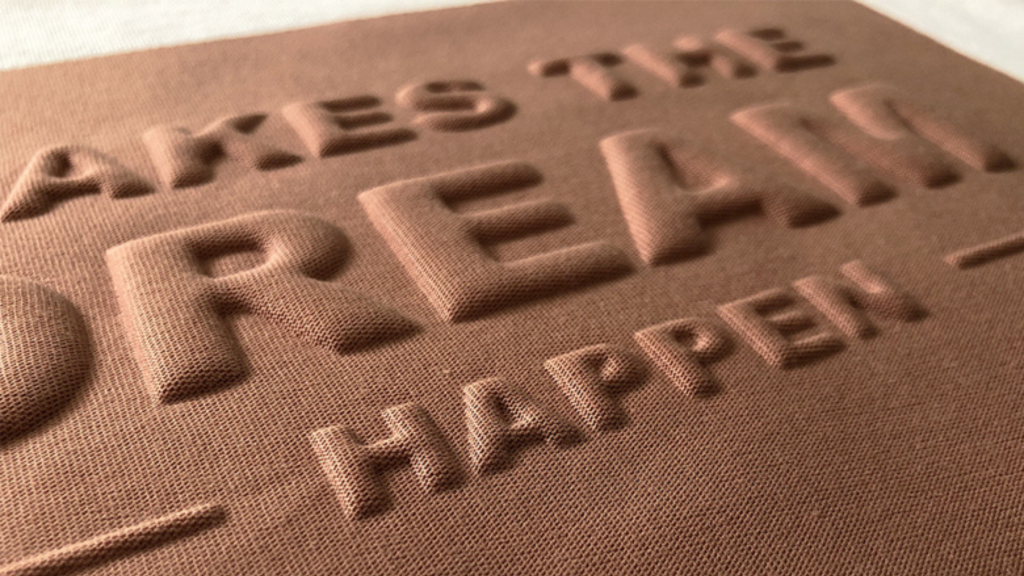
In short, each technique has its own characteristics and benefits, and the choice of the most suitable technique depends on the type of fabric, the desired end product and the cost and time available for production at Simetex all techniques are carried out with the utmost professionalism and quality.